
RFIDの活用で
誤出荷ゼロを実現
アパレル企業の多くが、最初は自社倉庫から始まり、一定の店舗数に出店が増えた段階で、物流業務をアウトソーシングに切り替えることが一般的です。そうなると手元に商品が無いために、営業、マーケティングの商品理解力が各段に力を失うことがままあります。故に自社倉庫を重要ととらえる企業も多く、そんな企業が抱えるジレンマとして、出荷規模増と人員増、作業精度の悪化が問題となります。今回の婦人服のアパレル企業も同じようなジレンマを抱えていましたが、幸いなことにRFIDという商品を読み取る機械が導入されており、そこに活路を見出すことが出来ました。

1.目覆う状況からのスタート
お客様担当者とのヒアリングは目を覆う状況からのスタートでした。
たくさんあった課題のうち、大まかなものは以下の4つ
①入荷作業と出荷作業を同じスペースで実施しており、午前中に入荷作業を行い、入荷したものを午後に出荷作業を行わないと、翌日の入荷スペースがなくなることに。当日入荷、当日出荷が前提の物流泣かせの現場!
②当日検品後の商品を棚戻しするスペースがないため、店舗の振り分けは事前に段ボールを配置し、出荷店舗別に検品後にピッキングと配分を同時に行う必要があり、入荷をシステムに入れた後にピッキングリストを出す作業が手間になっている。効率よく実施しないと、商品を振り分けるスペースが足りなくなる
③配分数については、営業が直前まで当日の売上状況を確認しながら変更しているため、ピッキング直前まで最終値が変動している状態で、一度振り分けた商品を再度振り分ける必要が出た場合に、段ボールの中身をひっくり返すことになり非常に面倒。正確に営業が望んでいる在庫配分の精度とはならず、誤出荷を無くすことができていなかった。
④狭いスペースに段ボールを並べて配分する作業の中、商品量が段ボールの容量を超え雪崩をうって隣の段ボールと混ざってしまうなどの事象に気づかずに出荷してしまうことも。本来なら配分した結果が正しいか再度商品を確認する作業を行うのが望ましいが、配送時間の制約で実施できていないのが実情。
といった、おおよそ倉庫業務が正常に機能しているとは言えない状況のなかで運用を行っており、早急に対応する必要がありました。
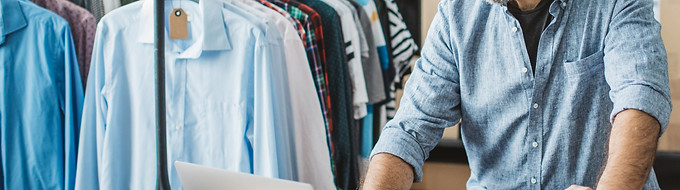
2.対応方針の確認
まず対応方針の確認です。
どう考えてもアウトソーシングしたほうが、簡単に解決できます。
当然ながらお客様自身も、実際に、何度も業者に依頼することを検討しており、他のベンダーも同様の提案にとどまっていました。
この企業の強みは、店舗で売れている商品をクイックレスポンスで仕入、店舗に展開する事なのは間違いなく、アウトソーシングでは、根本の自社倉庫の強みを生かすことに繋がらないため、課題を見て見ぬふりをしていた状態でした。
そこで下記の前提条件で実現できる案を模索することに。
①自社倉庫を上手に活用
②誰でも簡単に作業が可能
③出荷作業量の上限を拡大
④誤出荷を無くし、出荷精度を高めることができること
なかなか難しいオーダーです。

3.RFIDの技術が解決の糸口に
現状のシステムリソースを調べていく中で、中小企業には珍しくRFIDのタグとスキャナを導入していました。ただ活用自体は棚卸の作業にしか利用しておらず、あまりメリットを出せていない状況でした。
RFIDの利点は、基本的に商品の個体を識別管理しており、商品数量を正確に把握する場合に、商品1つ1つを明確に確認することが可能な仕掛けです。
棚卸を行うときは商品数量だけを管理すれば良いのでシステム化が簡単に行え便利ですが、販売管理システムと連動させようとすると、商品を管理する個体識別情報をシステムにマスタ登録する必要があります。商品に事前にタグ付けされて納品される形式の場合は、1商品ごとに登録することになり、時間がかかるため販売管理システムとの連動が課題となりました。
ただし機器導入が無いことは、次のステップに行くハードルを下げてくれました。
・RFIDの端末を利用しており、倉庫、店舗ともに導入が完了していた
・商品タグにRFIDのタグが導入されており、タグ業者と商品仕入先とが既に連携されて運用が回っていたため、取引先側の運用変更が不要。
このRFIDを利用することで、入力の手間と精度UPの課題を解決できないか。。。解決策を模索します。
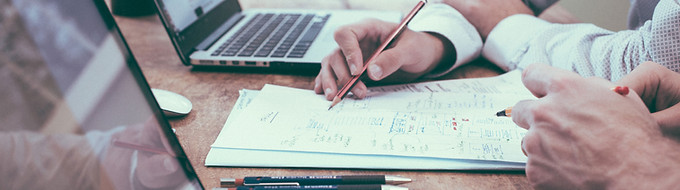
4.逆転の発想と理解あるユーザーとのコラボ
今回のケースは、課題は難題ですが、ユーザーのやりたいことがはっきりしており、考え方の優先順を変えられたことが、成功の秘訣でした。
まず、やりたいことは、
①作業効率の向上
②在庫精度の向上
です。
我々の提案は、根本的な考え方の発想を変えることから始めました。
①倉庫ではきちんと作業をしようとすればするほど時間とコストがかかってしまうため、全部の解決自体をあきらめ、部分解決を優先する。
②結果的に在庫が合えば問題ない。
この段階だと何を言っているかわかりづらいかもしれません。
整理すると、
①入荷時はRFIDが商品についているため、全商品を個体レベルで正確に把握すること。
②通常は出荷時に正しい出荷を求められるが、作業時間効率化のために、正しさ自体を求めない。(究極間違っていてもよい)
③店舗は、自店舗に入庫された商品が全商品わかるため、個体レベルで正確に把握すること。
④売上を上げるとき(在庫が自社からなくなるとき)は、個体レベルで把握すること。
上記の4点の考え方をまず理解してもらうことが重要となりますが、なかなか通常の企業では『正しくなくても良い』とはなりません。
今回は企業側の柔軟な理解度が成功につながります。

5.RFIDの資産を生かす課題解決
先ほどの考え方をもとに今回の課題の解決を図ります。
①倉庫や店舗では、初めての入荷商品はRFIDのタグ情報がシステムに登録されていないため、RFID情報を読み取ることが出来ず、読みとり機器のエラーとなります。ここで逆転の発想です。
読み取った情報をエラーとしてではなく、正常の新入荷情報とできないか。実際に読みとり機器からは、エラーのログ情報としてRFIDの情報が出力されるのが分かり、その情報を新入荷情報として取り込むシステムを構築しました。
これにより商品が倉庫に到着したときにまず入荷作業をRFIDの機器で読みとりを行うだけで、新入荷情報となるため、確認と登録作業が各段に効率化することができ、合わせて精度もアップしました。
<入荷時にRFIDをもとに全商品を個体レベルで正確に把握すること>
②次に、出荷作業は今まで通り実施し、極力システムへの入力作業を無くすため、ピッキングリストの出力=出荷の確定なるシステムとしました。(仮の個体識別での移動としてシステム的な処理を実装)
仮に出荷数が間違っていても訂正は行わず、出荷作業を優先します。
<ピッキングリスト出力=出荷の確定>
③店舗は、新入庫情報としてRFIDを読み取りますが、入荷と違うところは、既にシステム内にRFID情報として登録されているため、エラーとはなりません。ここでも逆転の発想です。
個体レベルで商品のRFID情報が読み取ることが出来るので、商品自体は正しく現地に存在していることが証明されています。そのため間違っているのがシステムだという認識のもと、もともとあったRFIDの情報を正しい店舗に入庫されたという情報として扱うシステムを構築することで、入荷したときに常に正しい在庫が自動的にシステムに反映されることを実現しました。
<入庫時にRFID情報をもとに、自店舗在庫を正常にする>
④RFID情報と商品と紐づきを正常に保つためには、商品を販売したときに、正しく該当の個体識別情報の在庫を減らす必要があり、システム的にも工夫することにしました。
商品を読み取る機器が通常のスキャナでもできるように、バーコード情報を個体識別の番号でも読み取ることが出来るようにしました。
また仮にその商品が店舗に未入庫だった場合には、入庫と同じように自動的に反映させる制御。未入荷だった場合には、仮個体識別番号を採番し、次回入荷時に消し込む機能をシステム化することで、常に正しいRFID情報を実現し、商品とシステム在庫情報を正常化させることに成功しました。
これにより、仮に倉庫が間違った出荷をしても、店舗が未入庫のものを販売しても、翌日には正しい在庫になり、運用上に問題を起こさず、手間をかけずに在庫精度を解決したいという当初の難題を解決することできました。

6.解決後にも好影響を。。。
個体識別で在庫を管理することが出来た結果、棚卸の精度が個体単位で行うことができるため、ロス調査がスムーズに。
また個体識別での商品の移動状況をきちんと把握することができるため、無駄な店間移動を減らすことにも繋ぐことができています。
如何でしたでしょうか?
このように、問題だらけの状態から、一番難しい在庫精度であったり、在庫移動の効率化を実現するシステムの構築は、
ユーザーの悩みから、その課題を解決するまでの『構築に対する理解』があることで、素晴らしい結果に繋がります。
我々が解決に向けて全力でサポートします。
是非、一度、自社の課題を相談してみませんか?